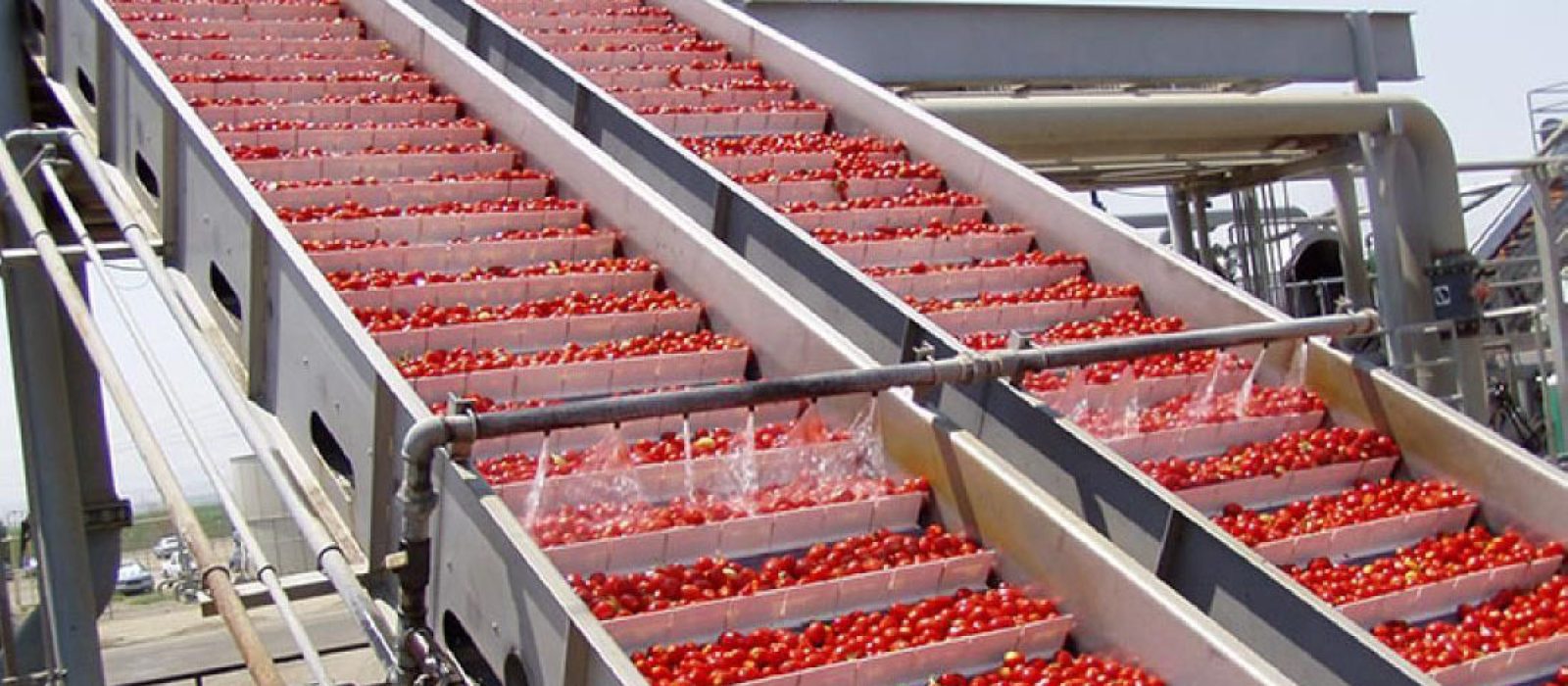
Case Study: How a Capped Edge Conveyor Belt Helped A Vegetable Supplier Cut Costs
A vegetable supplier in Illinois was experiencing issues with frayed edges on their conveyor belts. The rough, frayed edges were causing issues during their Safe Quality Food Audits.
The company's puree and juice lines start with bins of vegetables being dumped into a hopper. The product is then sent via conveyor belts to mills, strainers, pasteurization, and blending processes. The degree to which the product is reduced is determined by the product requirements (i.e. diced, unfiltered or filtered juices, or purees).
The Challenge
While the belts performed well in regard to durability, the constant exposure to water and uneven loads from vegetables shifting, caused rubbing on the edges of the belts which created fraying. This fraying was a problem for the company's Safety Quality Food Audits.
The Solution
The customer contacts Sparks Belting seeking options for a solution to their fraying problems. It was decided that a cast urethane-capped edge on the belt would get the job done. In addition to the cast urethane-capped edge, it was determined that a slight indent on the cleat would help with belt rubbing as well.
The Outcome
Typically, fraying of the conveyor belt edging would begin within the first several months of operation. There was no fraying in this time frame with the new capped edge belts, exceeding the customer's expectations. Since the belts were lasting much longer, the customer was saving money and reducing downtime on replacement belts. Their Safe Quality Food Audit outcomes were much better than they were before the new belts and the vegetable supplier is now operating at a level 3 rating- the highest a company can receive.
All Blog Posts
Need help solving a problem with your conveyor belts? We can help.
Contact a Representative Today