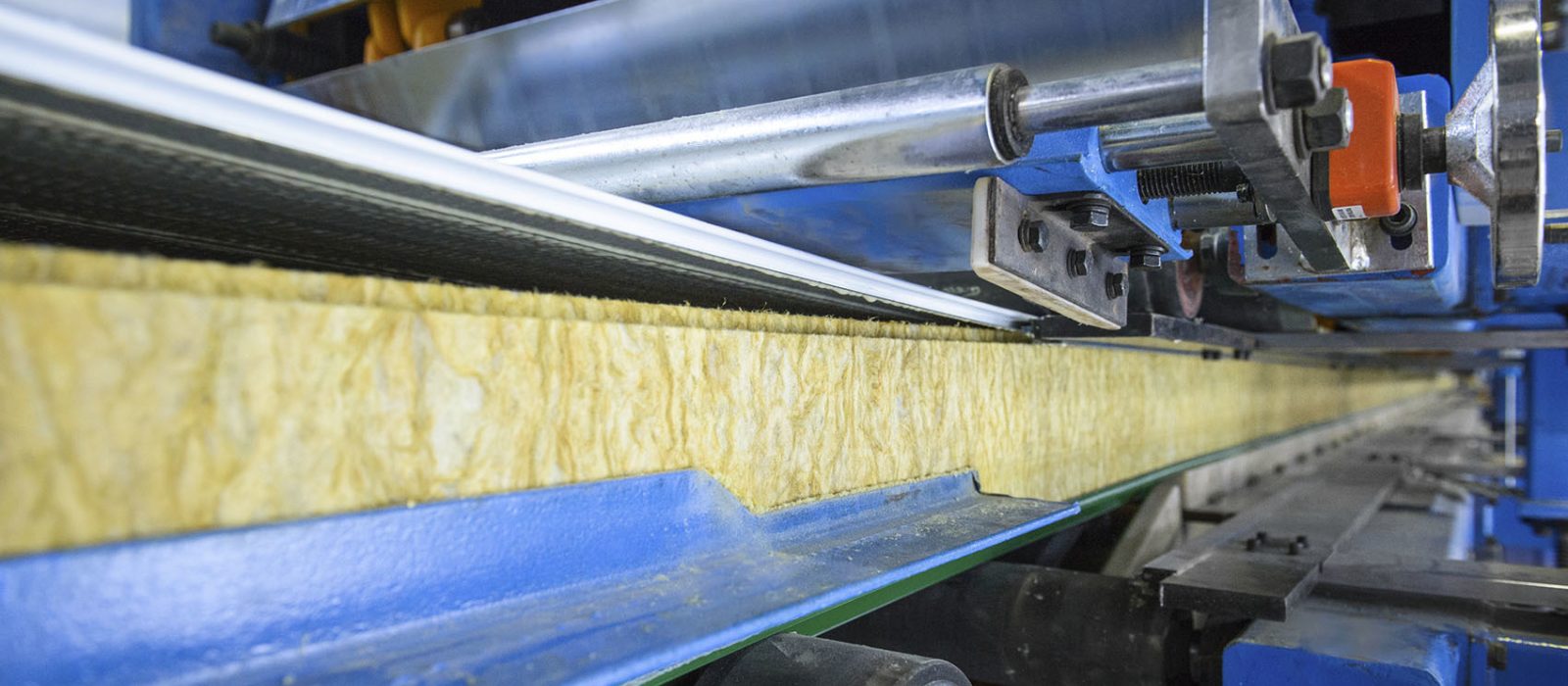
Case Study: How a High Grip Conveyor Belt Helped a Manufacturer Reduce Slipping and Downtime
Louisiana Pacific Corporation is a leader in the engineered wood products industry. They were having issues with their building materials slipping on their conveyor belt. Sparks was able to come up with a solution to solve their issues as well as save them downtime.
The Company
Louisiana Pacific Corporation is a leader in the engineered wood products industry. They grind up logs into 2-4” size chips to make a product called SmartSide® trim and siding for houses. This product starts out as a 6” thick mat of wood chips, which is then impregnated with a variety of binders, insect inhibitors, etc. The mat of wood chips is then compressed into standard wood shapes and profiles. The final product is about 3/4” thick engineered wood siding that replaces cedar lap siding, plywood sheet siding, and cedar trim boards.
The Challenge
Louisiana Pacific had been using carboxylated nitrile on a 72” wide conveyor. This belt turned out to be too slippery which was causing the sheets or boards of SmartSide® to slip around the belt when driven to the next processing stage.
The Solution
Sparks decided to switch the current LP belt to an Econo Ruff Tan belt which has high gripping capability. The team at LP really liked the better gripping of this belt. By switching to a softer cover rough top that can handle some abrasion, better grip without premature wear was achieved. The product has been performing very well.
The Results/Outcome
By having better cover “grip” with this belt, it keeps the boards or sheets from jamming up as they transfer, which prevents downtime. Sparks was able to solve the slipping issue for Louisiana Pacific by applying the correct product to the application. The customer is planning to switch more applications to this new belt due to better gripping and fast lead times.
All Blog Posts
Talk to a Sparks Representative Today For Your Custom Solution
Contact Us