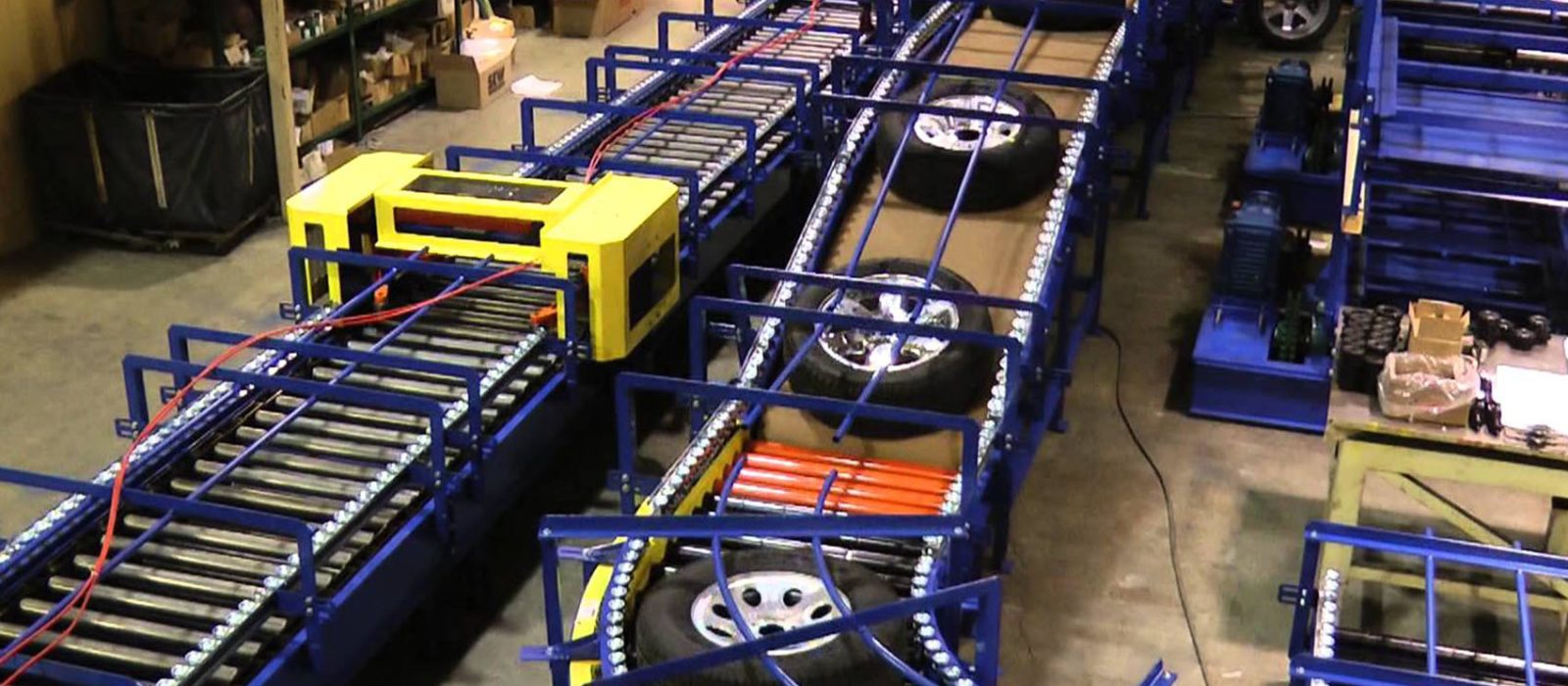
Case Study: How a Rubber Conveyor Belt Increased Belt Life Reducing Maintenance Costs and Downtime
A tire retread facility in Covington, Georgia reached out to Sparks Belting to help solve a slipping issue with their conveyor belts. The company is a leader in the tire retread industry with millions of tires on the road across North America.
The Challenge
The tire retread company was having trouble with their uncured rubber material slipping on their belts. A build-up of lubricant for the tire material, along with pressure from brushes that clean the uncured rubber was causing tracking issues and the V-guides on the belt to come off. They were looking for a new belt with the right amount of grip and greater durability to improve their application.
The Solution
After testing a piece of the uncured material against samples of Sparks’ belting our team came up with an offering of several choices as a solution including; Red Rubber Ribbed (RRR) belting and notched Urethane V-guides.
The tire retread facility decided to test the Red Rubber Ribbed belt with a notched Urethane V-guide. They were so pleased with the results, they ordered replacement belts for all of their retread conveyors. The facility also ordered the same material for some of their other conveyors.
The Results/Outcome
The retread facility reported that they were receiving approximately 1-2 months out of their previous belts. The new belts that Sparks supplied have lasted 5 months to date with no problems whatsoever.
All Blog Posts
Looking to Upgrade Your Conveyor Belts to Cut Maintenance Costs?
Contact Us Today!